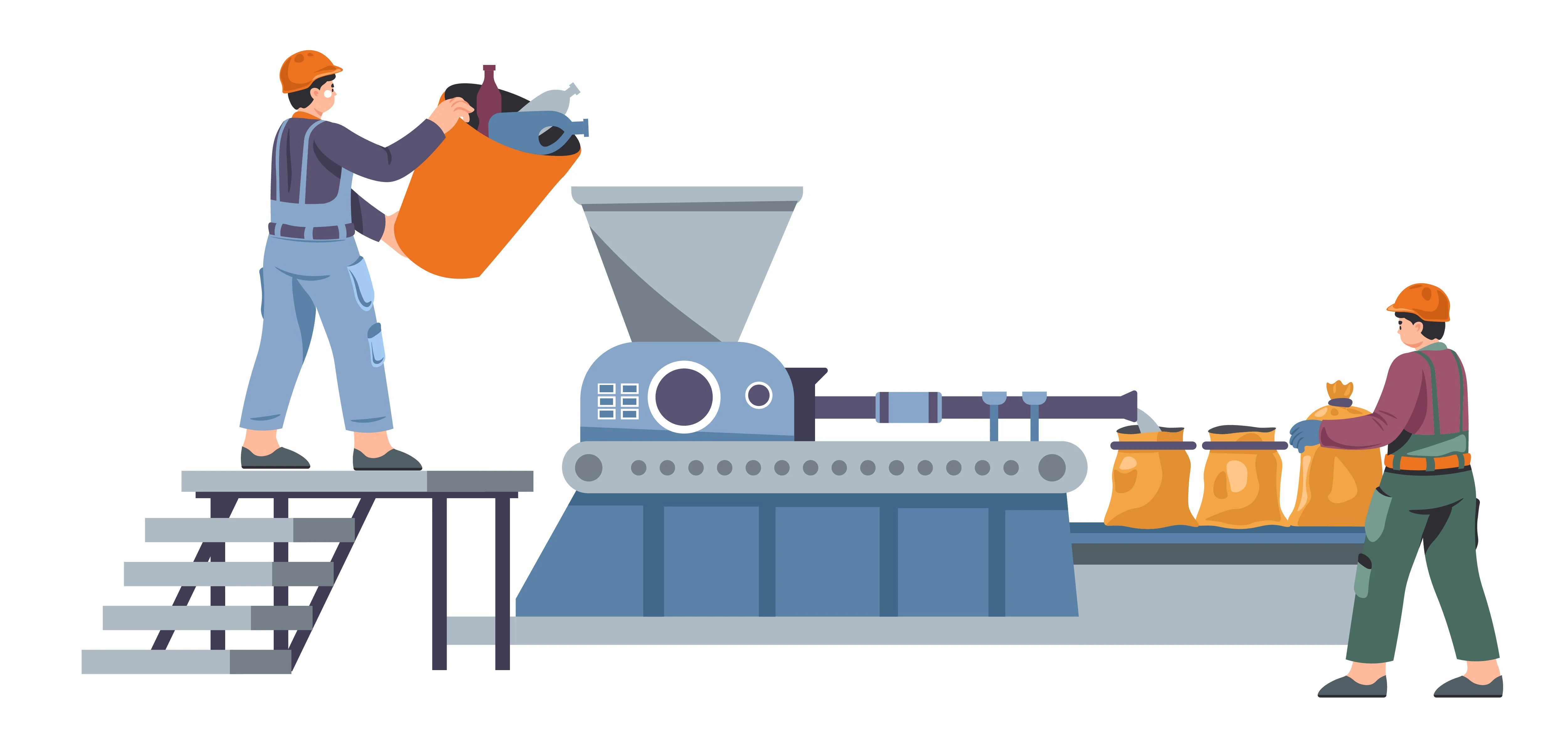
Microsoft Business Central for Plastics Industry
In the rapidly evolving landscape of the plastics industry, companies are continually seeking innovative solutions to enhance operational efficiency, streamline processes, and maintain a competitive edge. Microsoft Business Central emerges as a pivotal tool, tailored to meet the intricate demands of this sector. As a comprehensive, cloud-based enterprise resource planning (ERP) solution, it seamlessly integrates various business functions, offering unparalleled visibility and control over operations. The plastics industry, with its unique challenges such as fluctuating raw material costs, stringent regulatory requirements, and the necessity for precise inventory management, demands an ERP system that is both robust and flexible. Microsoft Business Central provides a platform that not only addresses these challenges but also empowers businesses to optimize supply chain management, improve production planning, and enhance customer relationships. By leveraging advanced analytics and real-time data insights, companies can make informed decisions that drive growth and sustainability. Furthermore, its scalable architecture ensures that as the business grows, the technology infrastructure can adapt, supporting continuous innovation and improvement. This article explores how Microsoft Business Central is revolutionizing the plastics industry by providing a strategic framework for businesses to thrive in an increasingly competitive environment.
Streamline Operations with Business Central
Utilizing Business Central allows companies to enhance their operational efficiency by integrating various business processes into a unified system. This advanced platform provides real-time data access and analytics, enabling organizations to make informed decisions swiftly and effectively. By automating routine tasks and optimizing workflow, businesses can significantly reduce operational bottlenecks and focus on strategic growth initiatives. The seamless connectivity between departments such as finance, supply chain, and customer service ensures a coherent flow of information, thereby reducing errors and improving overall productivity.
Furthermore, the scalable nature of Business Central means that it can evolve alongside the business, accommodating growth and changes within the industry. Customizable modules allow companies to tailor the system to meet specific operational needs, ensuring that the software remains relevant and effective. The integration capabilities extend beyond internal operations, facilitating better collaboration with external partners and suppliers, which is critical in maintaining a competitive edge. This adaptability and functionality make Business Central a vital tool for businesses seeking to streamline operations and drive growth in a constantly changing market environment.
Streamline Operations with Business Central
- Automate inventory management to reduce manual errors.
- Optimize production schedules for improved efficiency.
- Integrate financial systems for real-time data access.
- Enhance customer relationship management processes.
- Streamline supply chain operations for better coordination.
- Utilize advanced reporting for informed decision-making.
Enhance Inventory Management Precision
Precise inventory management is crucial for maintaining a competitive edge, especially in the plastics industry where supply chain dynamics can be particularly complex. Leveraging advanced functionalities within Business Central facilitates accurate tracking of inventory levels, enabling businesses to optimize stock levels and reduce waste. By implementing real-time inventory monitoring, companies can swiftly respond to fluctuations in demand, minimizing the risk of stockouts or overstocking. This not only increases operational efficiency but also enhances customer satisfaction by ensuring timely availability of products.
Additionally, the system's robust analytical tools provide deep insights into inventory performance, helping identify trends and areas for improvement. Automated alerts and intelligent forecasting assist in proactive decision-making, allowing businesses to adjust purchase orders or production schedules as needed. The precision offered by Business Central translates into financial savings and improved resource allocation, driving profitability while maintaining a consistent supply chain. By focusing on accurate inventory management, organizations can streamline operations and focus on strategic growth initiatives within the plastics sector.
Enhance Inventory Management Precision
- Implement real-time inventory tracking for accurate stock levels.
- Automate reordering processes to avoid stock outs and overstocking.
- Utilize barcode scanning for efficient inventory data input.
- Integrate demand forecasting to optimize inventory planning.
- Monitor inventory locations for streamlined warehouse operations.
- Generate inventory reports for informed decision-making and analysis.
Optimize Production Workflow Efficiency
Maximizing production workflow efficiency is crucial for maintaining competitive advantage and driving growth in the plastics industry. By streamlining processes and eliminating bottlenecks, companies can significantly reduce production times and costs. Implementing an integrated system that provides real-time visibility across all stages of production enables teams to monitor progress closely and identify areas where efficiency can be enhanced. With real-time data, decisions can be made swiftly, ensuring that resources are allocated optimally and potential disruptions are minimized.
Moreover, the automation of routine tasks within the production workflow not only frees up valuable human resources but also reduces the likelihood of errors, thereby improving overall product quality. Advanced scheduling tools and resource planning capabilities contribute to more effective coordination between departments, ensuring that each stage of production is aligned with overall business goals. This holistic approach to managing production workflows can lead to increased output, reduced waste, and better utilization of machinery and labor, ultimately resulting in a stronger bottom line for companies in the plastics sector.
Optimize Production Workflow Efficiency
- Implement automated scheduling for resource allocation.
- Streamline communication between production teams and management.
- Utilize real-time data analytics for process monitoring.
- Reduce waste through lean manufacturing principles.
- Enhance inventory management with accurate forecasting.
- Integrate quality control into every production stage.
Seamless Integration with Existing Systems
Incorporating new technology into existing operations often poses significant challenges, particularly concerning compatibility and disruption of current processes. However, achieving a successful integration with existing systems is paramount to leveraging the full potential of any new solution. Ensuring that the new system communicates effectively with legacy systems and databases can enhance data accuracy and continuity, fostering a more cohesive operational environment. This seamless connectivity not only facilitates better data flow and reduces duplication but also empowers organizations to maintain continuity in their operations without requiring extensive retraining of personnel.
Furthermore, the ability to integrate seamlessly with existing systems helps organizations in the plastics industry to uphold regulatory compliance and maintain customer satisfaction by ensuring consistent quality and service delivery. By providing a unified platform that consolidates data from various sources, businesses can gain comprehensive insights into their operations, enabling them to make informed decisions swiftly. This cohesive integration also supports scalability, allowing organizations to adapt to changing market demands without overhauling their entire IT infrastructure. By aligning new capabilities with existing processes, companies can achieve operational harmony, thereby optimizing performance and driving sustainable growth.
- Easy data transfer between new and existing software solutions.
- Compatible with legacy systems for smooth operational continuity.
- Minimal disruption during system updates and maintenance.
- Supports various file formats for seamless communication.
- Streamlined workflow through integrated data processing.
- Facilitates real-time data synchronization across all platforms.
Improve Cost Control and Analysis
Enhancing cost control and analysis within the plastics industry involves developing a sophisticated understanding of the intricate production processes and material requirements. By utilizing comprehensive data analytics, organizations can meticulously track material usage, labor costs, and machine efficiency to identify areas for potential savings. Implementing detailed cost-tracking mechanisms allows businesses to pinpoint inefficiencies, predict budgetary needs, and adjust procurement strategies accordingly. This approach not only optimizes resource allocation but also supports strategic planning, enabling companies to respond agilely to market fluctuations and raw material price changes.
In addition to monitoring direct production costs, it is crucial to examine overhead and indirect expenses to gain a holistic view of financial health. By adopting a robust cost analysis system, management can perform real-time financial assessments, facilitating more informed decision-making. This precision in financial oversight assists in setting competitive pricing strategies while maintaining profitability margins. Organizations that prioritize cost control and analysis are better positioned to invest in innovation and sustainability initiatives, ultimately enhancing their competitive edge and fostering long-term growth in an increasingly dynamic market.
Improve Cost Control and Analysis
- Implement real-time cost tracking for accurate financial insights.
- Utilize data analytics to identify cost-saving opportunities effectively.
- Automate cost reporting for improved decision-making and efficiency.
- Monitor inventory levels to reduce excess stock and costs.
- Streamline procurement processes to minimize purchasing expenses.
- Conduct regular financial audits to ensure budget adherence.
Real Time Data for Better Decisions
Real-time data provides immediate insights into operational performance and financial metrics, allowing management to swiftly identify trends and anomalies. This dynamic approach ensures that any deviations from expected performance can be addressed promptly, minimizing potential disruptions. By leveraging real-time information, decision-makers can enhance operational efficiency and capitalize on emerging opportunities more effectively. This capability is particularly vital in the rapidly evolving plastics industry, where timely decisions can significantly impact competitiveness and profitability. The integration of real-time data analytics into business operations empowers organizations to maintain a proactive stance, fostering a culture of continuous improvement and innovation.
Real-Time Data Benefits
- Improves operational efficiency with timely insights.
- Enhances decision-making for production processes.
- Identifies trends and patterns in data promptly.
- Reduces downtime by predicting maintenance needs.
- Optimizes inventory management for cost savings.
- Increases customer satisfaction through quick response times.
Boost Customer Relationship Management
Enhancing customer relationship management is crucial for achieving long-term success in the plastics industry. By utilizing advanced CRM tools, businesses can gain a comprehensive understanding of customer needs and preferences, leading to more personalized and effective interactions. This approach not only helps in retaining existing clients but also in attracting potential new customers through tailored marketing strategies. Furthermore, leveraging CRM solutions enables companies to streamline communication channels, ensuring that customer inquiries and concerns are addressed promptly and efficiently. This level of responsiveness builds trust and strengthens relationships, ultimately contributing to improved customer satisfaction and loyalty. In a competitive market, where customer expectations are continually evolving, a robust CRM system is indispensable for maintaining a competitive edge.
Boost Customer Relationship Management
- Implement personalized communication strategies for customer engagement.
- Utilize data analytics to understand customer behavior and preferences.
- Automate routine tasks to enhance customer service efficiency.
- Integrate CRM systems with existing business processes and tools.
- Offer training programs to improve customer interaction skills.
- Gather customer feedback regularly to improve service offerings.
Scalability to Support Business Growth
As businesses in the plastics industry strive for growth, the ability to scale operations efficiently and effectively becomes paramount. Scalability is not merely about expanding production capabilities but also about enhancing the overall infrastructure to support increased demands. This involves optimizing supply chain processes, ensuring robust data management systems, and implementing adaptable software solutions that can grow in tandem with the business. By focusing on scalable solutions, companies can seamlessly manage larger volumes of orders, diversify product lines, and enter new markets without compromising on quality or operational efficiency. A scalable approach also enables businesses to respond swiftly to market changes and customer demands, ensuring sustained growth and competitiveness in the dynamic landscape of the plastics industry.
Scalability for Business Growth
- Adaptable software to meet growing business needs
- Efficient data management for expanding operations
- Seamless integration with existing business systems
- Flexible cloud solutions for scalability and efficiency
- Scalable infrastructure to support increased production demands
- Automated processes to streamline business growth efforts
Enhance Supply Chain Collaboration
To drive substantial improvements in supply chain performance within the plastics industry, fostering robust collaboration among all stakeholders is essential. Effective collaboration facilitates a seamless flow of information, enabling real-time visibility into inventory levels, production schedules, and logistics. This transparency helps in mitigating risks, reducing lead times, and improving overall responsiveness to market dynamics. By leveraging integrated platforms, stakeholders can align their objectives, share critical insights, and make informed decisions that enhance supply chain agility and efficiency. Furthermore, enhanced collaboration strengthens supplier relationships, allowing for more strategic sourcing and better negotiation outcomes, ultimately contributing to cost reductions and increased service levels. This collaborative approach not only optimizes operational workflows but also drives innovation, encouraging the development of more sustainable and cost-effective solutions.
Enhance Supply Chain Collaboration
- Implement real-time data sharing across all stakeholders.
- Foster transparent communication between suppliers and manufacturers.
- Utilize integrated platforms for streamlined order management.
- Establish clear roles and responsibilities within partnerships.
- Encourage feedback loops for continuous process improvement.
- Align goals and metrics for mutual success.
Regulatory Compliance Made Easier
In the plastics industry, navigating the complex landscape of regulatory compliance is a critical yet often challenging task. By integrating advanced business management solutions, companies can streamline compliance processes, reducing the risk of non-compliance while saving valuable time and resources. These solutions offer automated monitoring and reporting features that ensure adherence to industry regulations and standards. They provide real-time access to regulatory updates, enabling businesses to rapidly adapt to changes and maintain compliance with minimal disruption. Additionally, the digitization of documentation and processes simplifies audits and inspections, ensuring that all necessary documentation is accurate and readily accessible. This not only enhances operational efficiency but also fortifies the company's reputation by demonstrating a commitment to ethical and lawful practices.
Regulatory Compliance Simplified
- Automated reporting for compliance documentation
- Real-time tracking of regulatory changes
- Integrated audit trail features
- Customizable compliance checklists
- Centralized data management for regulations
- User-friendly interface for compliance navigation
Microsoft Business Central offers a robust and comprehensive solution tailored for the complexities of the plastics industry. By integrating essential business functions such as supply chain management, production planning, and financial reporting into a single platform, it empowers organizations to enhance operational efficiency and drive innovation. With its scalable architecture and user-friendly interface, Business Central not only addresses current industry challenges but also positions companies for future growth. As the plastics industry continues to evolve, leveraging such advanced technological solutions will be crucial in maintaining a competitive edge and achieving long-term success.
FAQ - Frequently Asked Questions
- How can Microsoft Business Central optimize inventory management for the plastics industry?
- What features in Business Central support production scheduling and tracking for plastics manufacturing?
- How does Business Central facilitate quality control and compliance with industry standards in plastics?
- Can Business Central integrate with existing supply chain systems specific to the plastics sector?
- What tools does Business Central offer for financial analysis and cost management in plastics production?
How can Microsoft Business Central help streamline the supply chain management processes for companies in the plastics industry?
Microsoft Business Central can streamline supply chain management for companies in the plastics industry by providing integrated tools for inventory management, demand forecasting, and production planning. It enables real-time visibility into inventory levels, helping to optimize stock and reduce waste. The platform facilitates seamless communication across departments, ensuring timely procurement and order fulfillment. Its analytics capabilities allow for data-driven decision-making, enhancing efficiency and reducing costs. Additionally, Business Central can automate routine tasks, improving accuracy and freeing up resources for strategic initiatives, ultimately leading to a more responsive and agile supply chain.
What specific features of Microsoft Business Central can assist plastics manufacturers in managing inventory levels and tracking raw materials?
Microsoft Business Central offers several features to assist plastics manufacturers in managing inventory and tracking raw materials. It provides real-time inventory tracking, ensuring accurate stock levels and reducing waste. The software supports automated reordering, helping maintain optimal inventory by setting reorder points and quantities. It also offers comprehensive reporting and analytics to forecast demand and optimize supply chain operations. Additionally, Business Central enables batch and lot tracking, ensuring traceability of raw materials throughout the production process. These features help manufacturers maintain efficient operations, minimize costs, and enhance overall productivity.
In what ways can Microsoft Business Central enhance production planning and scheduling for manufacturers dealing with diverse plastic products?
Microsoft Business Central enhances production planning and scheduling for manufacturers of diverse plastic products by offering real-time data integration, improved visibility, and streamlined processes. It enables efficient resource allocation by tracking inventory levels and production capacity, ensuring optimal use of resources. The system supports demand forecasting and automated scheduling, reducing lead times and minimizing stock outs. Customizable workflows and analytics improve decision-making, while integration with other Microsoft tools boosts collaboration and communication. Additionally, Business Central's scalability allows manufacturers to adapt to changing demands, ensuring flexibility in managing different product lines efficiently.
How does Microsoft Business Central support compliance with industry regulations and sustainability initiatives in the plastics sector?
Microsoft Business Central supports compliance in the plastics sector by offering integrated tools for managing regulatory requirements and sustainability initiatives. It provides real-time data tracking and reporting capabilities to ensure adherence to industry regulations. The platform's robust analytics and monitoring tools help companies minimize waste and optimize resource usage, aligning with sustainability goals. Additionally, it offers customizable workflows and automated processes to maintain accurate records and streamline audits. Business Central's integration with other Microsoft solutions enhances collaboration and transparency, enabling companies to efficiently manage environmental impacts and regulatory compliance in the plastics industry.
What reporting and analytics capabilities does Microsoft Business Central offer to help plastics industry stakeholders make data-driven decisions?
Microsoft Business Central offers robust reporting and analytics capabilities for the plastics industry through built-in dashboards, customizable reports, and integration with Power BI. These tools enable stakeholders to monitor key performance indicators, track inventory levels, and analyze production data in real-time. Users can generate detailed financial reports, assess operational efficiencies, and forecast demand trends. The system's flexibility allows for the creation of industry-specific reports tailored to unique business needs. By providing comprehensive insights and facilitating data-driven decision-making, Business Central helps stakeholders optimize resource allocation, improve supply chain management, and enhance overall business performance in the plastics industry.
Visit us - TechnicaX | Dynamics 365 Solution provider in the USA - https://technicax.com
#MicrosoftDynamicsBusinessCentral, #SupplyChainManagement, #PlasticsIndustry, #Innovation, #Sustainability